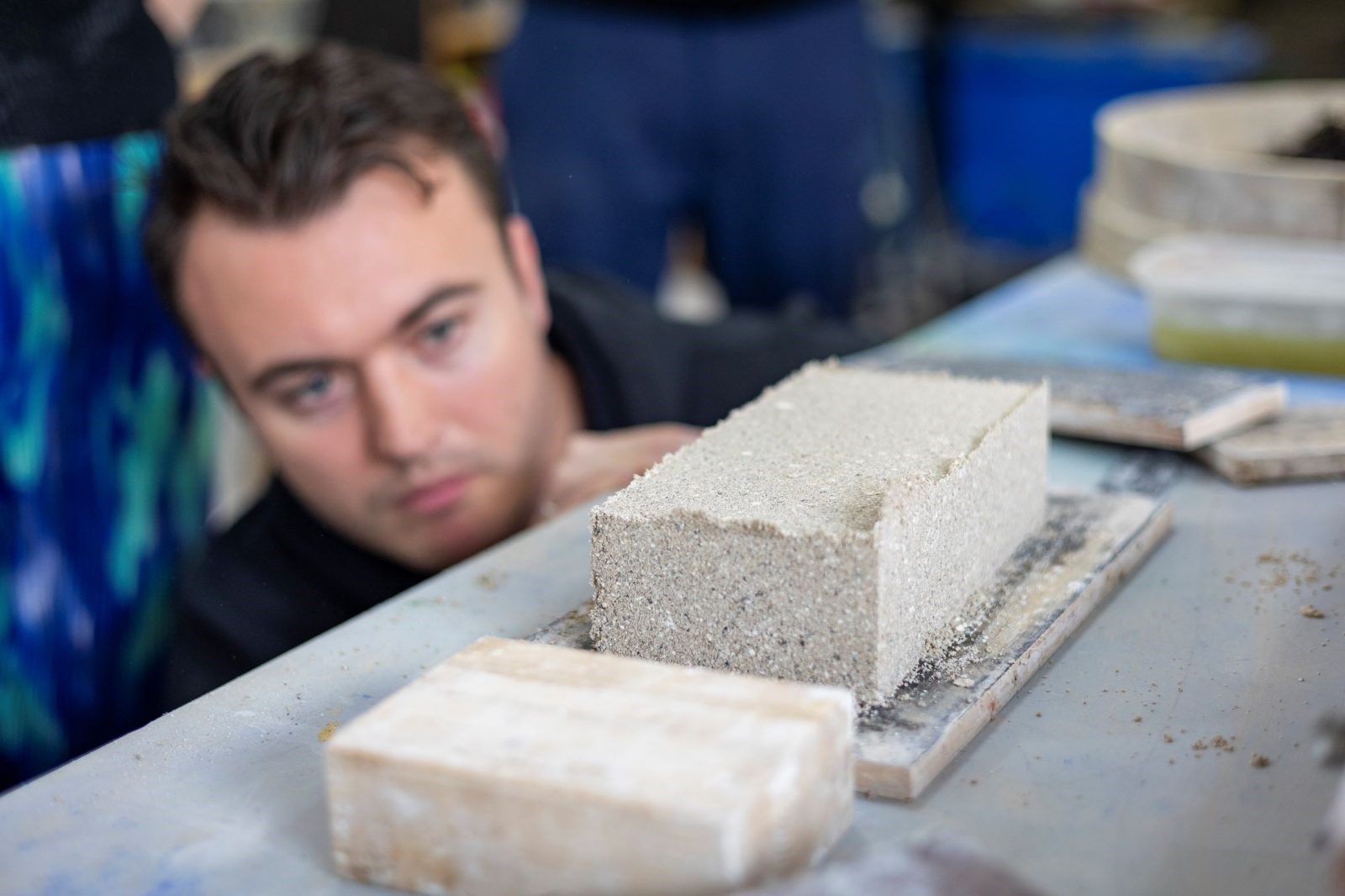
The innovative brick was produced as a result of 18 months of research funded by the Engineering and Physical Sciences Research Council (EPSRC) and the Higher Education Innovation Fund (HEIF).
Construction waste was used as aggregate
The company used magnesium carbonate as the binding material to produce the brick. The material was produced through a new process called carbon capture, mineralization and utilization (CCMU). Magnesium carbonate is produced from olivine, a mineral abundant throughout the world. The aggregate used in bricks was obtained from construction waste.
To put it simply, carbon dioxide released from industrial or other chimneys is captured and trapped inside the brick with the CCMU process. Thus, carbon dioxide is kept inside the brick instead of being released into the atmosphere, thus reducing emissions.
It cooks at a much lower temperature
Traditional bricks are manufactured at very high temperatures such as 1200 degrees. Seratech’s bricks are produced by firing at 60 degrees and waiting a little longer. The brick is baked overnight and strengthened by waiting for up to two weeks. Since it is fired at a much lower temperature, a more environmentally friendly brick is produced compared to traditional bricks.
“The magnitude of cement emissions is well known, but the emissions associated with clay-fired bricks, which are used in the millions every year in the UK, are rarely talked about,” says Seratech’s Chief Technical Officer, Barney Shanks.
The company is working with a London-based architectural team to commercialize the bricks they have developed. The initiative, which also received grant support from the Arts and Humanities Research Council (AHRC), wants to establish itself in the market as a commercially successful and widely used construction material.
Seratech’s Technical Manager, Caitlin Howe, said: “It’s incredibly exciting, and encouraging, to know that this is a product that could change an entire industry. Our bricks really look and feel like a traditional brick.” He speaks his words.